Dr B’s Midmark M9 Autoclave stopped working and was giving her the C983 error code.
Not sure what to do, she called a company and received a repair estimate of more than $1500.00. The estimate included a laundry list of items that the repair company said needed to be replaced to fix the problem.
Although she was unfamiliar with the parts listed to be in need of repair, it just did sound right to her. So, before giving the go ahead on the estimate, she decided to talk to AllClaveParts.com first.
We told her that based on the info she had given us; it was very unlikely that all the items on the list could be defective
We sent her the replacement vent valve. When she got it, she was both excited and apprehensive at the same time.
Could it really be as easy as we said for her to complete the repair?
After she removed the side panel, she opened the package and removed the new valve from the box. And then she called us right away. The vent valve did not look anything like the replacement valve we sent her.
In fact, the vent valve in her autoclave looked alien in comparison to the one we sent her
Based on the serial number, model number and error code, I knew we had sent the correct valve
So, I had her send us a picture of the valve she was replacing so I would know what we were working with
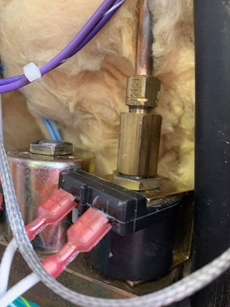
As soon as we saw the picture, we knew immediately what the problem was.
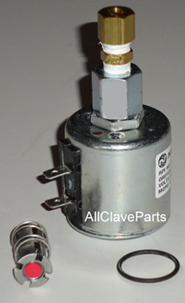
Here’s what happened:
For a short period of time, Midmark had used a different valve manufactured by Solenoid Solutions. Compared to the valves used before and after the run, these looked down right alien
After a short run, Midmark discontinued using those and went back to those offered by the Norgen & Kip Valve companies.
Support & replacements for the Solenoid Solutions valves were soon no longer available. So, did that mean the end of their autoclave?
Not hardly!
Here’s the solution:
It was simply a matter of replacing the vent valve with the one we had sent her for the newer autoclaves. Everything fits like it is supposed to. The only additional steps were to remove a little black box from the wiring that was located between the valve and the pc board
The box was placed there for a reason: The Solenoid Solutions Valve was not “FWR“ (Full Wave Rectified) which is required with the unit. The box was the rectifier & since the replacement valve we sent her is already FWR, the box had to be removed
DR B’s office had never attempted to do anything with their autoclave in the past, and they were frankly very scared to tackle it. But, after talking to us, they decided to give it a try
I got a call back a little later, telling me they had made the repair as we had directed and ran 3 successful cycles in a row.
She was so proud of herself, and miffed at the way the repair company had tried to take advantage of her with the ridiculous estimate for such a simple repair
AllClaveParts.com found the solution to her problem and sold her the exact valve she needed, and helped her to get her autoclave back in service very quickly….and no other parts were needed
We Helped Her Repair Her Autoclave….And We Can Help You Too!